Trong hàng nghìn năm qua, quá trình
sản xuất xi măng đã nung nóng các thành phần được sử dụng trong hỗn hợp liệu đến nhiệt độ cao nhất có thể để loại bỏ các tạp chất. Ngày nay, bột liệu hoặc nguyên liệu thô cho sản xuất xi măng portland được nung trong lò ~2000°F (~1000°C), giống như thả chúng vào tâm của một núi lửa đang hoạt động. Mặc dù, sau đó liệu sẽ trải qua một quá trình làm nguội, nhưng liệu tơi nhẹ vẫn còn đủ nóng để làm cháy thủng băng tải thông thường, các trang thiết bị bảo hộ cá nhân chịu nhiệt cao (PPE), hoặc rất nhiều thứ khác nữa mà nó gặp phải.
Sự hiện diện của liệu nóng từ lâu đã làm cho vấn đề an toàn trở thành vấn đề được quan tâm hàng đầu đối với nhân viên vận hành nhà máy xi măng. Tuy nhiên, cho dù đã có các biện pháp an toàn bảo vệ người lao động, nhưng việc giảm thiểu liệu tích tụ và sự cố tràn đầy ở khu vực nóng nhất trong quá trình sản xuất để tránh bị két tắc và dừng lò thường được xem là công việc khó khăn nhất trong toàn bộ nhà máy.
Nhân viên an toàn tại một
nhà máy xi măng ở Texas thường rất quan tâm đến điểm trung chuyển từ quá trình làm nguội đến băng tải nhánh (tripper conveyor) trong kho chứa clinker. Điểm trung chuyển bị ảnh hưởng rất lớn do liệu nóng tràn ra quá nhiều và gây ra rủi ro tiềm tàng cho người lao động. Đây là một vấn đề mà nhiều lần nhà máy đã cố gắng xử lý, với mục tiêu là giảm thiểu khối lượng công việc bảo dưỡng cần thiết liên quan đến việc sửa chữa và vệ sinh ở khu vực này. Dừng lò ngoài dự kiến, thất thoát nhân công và sản phẩm tăng lên đã làm tăng chi phí vận hành. Với việc làm cho hệ thống hoạt động hiệu quả hơn, nhà máy cũng hy vọng sẽ nâng cao độ an toàn xung quanh điểm trung chuyển.
Từ lò nung đến kho chứa
Trong quá trình xử lý gần 200 tấn bột liệu/giờ (181,4 tấn/giờ), clinker nóng chảy đi ra khỏi lò, và được chất tải lên băng tải tấm gồm một số tấm kim loại chịu nhiệt cao được kéo đi bởi một hệ xích. Gió lạnh nhanh chóng
làm nguội clinker, giảm nhiệt độ clinker từ khoảng 1400°F (760°C) xuống nhiệt độ 350 - 800°F (176 - 426°C).
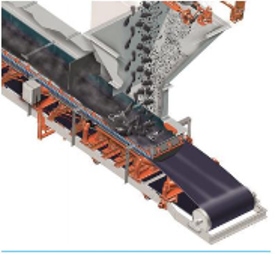
Điểm trung chuyển gốc đã gặp phải sự cố tràn liệu nghiêm trọng.
Ngay sau khi được làm nguội, clinker được xả qua một ống chute (ống tháo liệu) đặt nghiêng dài 5ft (1,5m) xuống một băng tải chịu nhiệt cao được nối với một băng tải nhánh treo phía trên cách các đống liệu lớn 80ft chạy dọc theo chiều dài của kho chứa clinker có kích thước rộng như kho chứa máy bay. Với chiều dài 1100ft (335m) và chiều rộng 24inch (610mm), băng tải vận chuyển liệu với tốc độ 260ft/m (1,32m/s) về phía ống tháo liệu nhánh.
Chuyển động chậm qua lại dọc theo toàn bộ chiều dài kho chứa, hệ thống băng tải nhánh có giám sát sẽ xả clinker qua một ống chute lên các đống liệu cao để tồn trữ. Liệu tồn trữ nhanh chóng được máy xúc gầu trước đưa tới các khu vực khác nhau trong nhà máy khi cần thiết.
Các vấn đề liên quan tới băng tải nhánh clinker cần phải được xử lý ngay, nếu không sẽ có thể gây ảnh hưởng tới sản xuất và khả năng đáp ứng các nhu cầu của khách hàng của nhà máy.
Cảm nhận thấy được nhiệt nóng
Một số vấn đề gây ra những lo lắng về an toàn tại nhà máy như điểm trung chuyển gốc từ băng tải tấm đến băng tải nhánh đã xảy ra sự cố liên quan tới độ làm kín. Liệu mịn nóng tràn ra hai bên và lắng đọng lại trên lối đi xung quanh. Ngoài ra, liệu tích tụ lại trong ống chuyển thường gây dừng sản xuất cho đến khi chúng được dọn sạch.
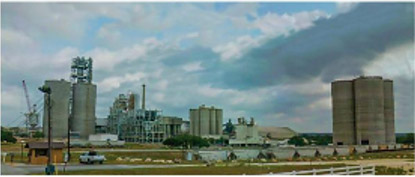
Nhà máy xi măng ở Texas.
Lối vào cũng là một thách thức. Cầu thang ngoài trời phải leo lên 8 tầng tới sàn thao tác, có thể là một công việc dễ gây nản lòng, đặc biệt là vào mùa hè ở Texas. Khi nhân viên đến được điểm trung chuyển, nhiệt độ ở đây tăng lên do nhiệt độ clinker gây ra. Việc dọn vệ sinh ống chuyển bằng tay sẽ tiếp xúc trực tiếp với liệu nóng, vì vậy, điều quan trọng là người lao động đã qua huấn luyện sử dụng mũi cắt bằng khí hoặc thiết bị phun khí CO2 để vệ sinh phải mặc PPE chịu nhiệt cao.
Để thu gom liệu tràn, một tấm lưới (grated shaft) 3x5ft (0,9x1,5m) đã được lắp lên sàn bên dưới điểm trung chuyển. Tấm lưới này dẫn xuống ống chute và đưa liệu xuống đống liệu tồn trữ ở bên dưới. Việc lắp tấm lưới này là nhằm mục đích giảm thiểu sự tiếp xúc liệu cho người lao động và tránh gây thất thoát sản lượng do tràn liệu. Tuy nhiên, liệu tràn quá nhiều vẫn chất đống xung quanh sàn, gây nguy hiểm tiềm tàng nên cần phải được vệ sinh dọn dẹp thường xuyên.
Ngay cả việc bảo dưỡng theo kế hoạch cũng đều phải quan tâm tới vấn đề an toàn và chi phí. Các nhà thầu thi công được đưa vào vệ sinh khu vực này khoảng hai lần một tháng. Một đội gồm 4 - 5 công nhân cùng với một xe téc chân không sẽ dọn sạch số liệu tràn này. Mỗi tháng, nhà máy phải chi trả cho công việc này lên đến 15.000 USD - 20.000 USD, tuỳ thuộc vào mức độ công việc và số lần đội vệ sinh phải vào làm.
Vật lộn với thiết bị
Điều kiện khắc nghiệt ở điểm trung chuyển này đã ảnh hưởng rất nhiều tới thiết bị. Các con lăn căng băng (idlers) thường xuyên bị kẹt hoặc bị nứt vỡ vì bị cong vênh do nhiệt gây ra, tải trọng của liệu vận chuyển, hoặc các hạt mịn mắc vào trong các chi tiết lăn như các ổ đỡ. Băng tải cũng sẽ bị mòn đi nhanh chóng, tạo thành các lỗ hoặc thậm chí bị nứt vỡ ở chỗ mối nối.
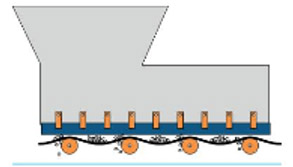
Phần đỡ băng không tốt khiến cho liệu mịn bay lơ lửng lắng đọng lên các con lăn căng băng, gây hỏng hóc sớm.
Lỗ lớn và tấm lưới bị cong vênh cho thấy hệ thống đã toả ra nhiệt độ rất cao.
Khi một con lăn căng băng bị mắc kẹt, nó sinh ra ma sát và nhiệt dư ở phía quay về (đáy) của băng. Ma sát có thể khiến cho băng nhanh chóng thoái biến và bị sờn các mép cạnh. Nếu để mặc nó không chú ý đến trong một thời gian dài, nó có thể mài mòn các chi tiết mối nối cơ học, làm cho mối nối bị đứt gãy. Mặc dù băng tải có thể phân bố nhiệt cao ở phía mang liệu, phía quay về lại dễ bị tổn hại nhiều hơn, có thể bị bốc cháy.
Các chi tiết dạng mô-đun được tích hợp với nhau mang lại hiệu quả tối đa.
Các con lăn chịu va đập được đặc biệt quan tâm đến, vì chúng có khả năng dễ bị kẹt nhất do tổn thất va đập và bị cong vênh do tiếp xúc với nhiệt liên tục. Các khe hở giữa các con lăn sẽ thường tạo thành các vết lõm và các vết nứt ở phía được bảo vệ của băng. Các điểm bị hư hại này sẽ không chịu nổi nhiệt và nhanh chóng tạo thành các lỗ. Do chi phí thay băng cao, các nhân viên vận hành sẽ bỏ mặc các lỗ này, cùng với sự cố tràn liệu cho đến khi không thể bỏ qua được nữa.
Phần làm kín băng ở các vị trí mang tải và lắng đọng liệu cũng là một vấn đề gây ra các sự cố tràn liệu. Các tấm lót chịu mài mòn dọc theo thành ống chute lại không hoàn toàn chịu đựng được môi trường nhiệt độ cao nên sẽ bị cong vênh hoặc bị rách, tạo ra các điểm trống cho các hạt mịn thoát ra. Các tấm chắn mép băng sẽ nhanh chóng bị mòn đi và để lại các khe hở lớn giữa các con lăn căng băng khiến cho băng bị võng xuống, dẫn đến thất thoát thêm liệu mịn bay lơ lửng ra ngoài.
Tìm ra giải pháp phù hợp
Lãnh đạo nhà máy đã không liên hệ ngay với Martin Engineering, và nhìn từ bên ngoài thì đó có vẻ như là một giải pháp hợp lý. Công ty đã cho lắp đặt một hệ thống đường ống tuần hoàn được gia công sẵn tạo ra một môi trường khép kín với lối vào thuận lợi cho bảo dưỡng và thay thế con lăn. Không may là, vật liệu thi công hệ thống đã không thể chịu được điều kiện môi trường khắc nghiệt và nhu cầu của hệ thống. Điều này đã gây ra sự cố tràn liệu quá nhiều, dừng thiết bị ngoài dự kiến, thất thoát sản phẩm và chi phí vận hành cao hơn. Do những hư hỏng và những lo ngại thực sự về hoả hoạn và an toàn, hệ thống đường ống cần được thay thế sớm.
Nhờ có mối quan hệ lâu năm, đã có một vài hợp đồng cung cấp dịch vụ và nhiều dự án thành công đã hoàn thành trong nhà máy này, Martin Engineering đã được mời vào kiểm tra điểm trung chuyển và đưa ra các giải pháp. Các kỹ thuật viên có trình độ tay nghề đã quá quen thuộc với các vấn đề liên quan tới kho chứa clinker thực hiện một chương trình Đi Bộ dọc theo Băng (BeltTM) mà đã giúp họ lập ra được một danh sách kiểm tra đầy đủ và xác định được các vấn đề trên toàn bộ quá trình trung chuyển.
Các kỹ thuật viên đã đề xuất một giải pháp Total Transfer Point SolutionTM năng suất cao hoàn toàn theo dạng mô-đun mà sẽ phù hợp hơn cho hệ thống. Giải pháp này bao gồm nâng lên và cắt ngắn phần bao che điểm trung chuyển, cải thiện đáng kể phần làm kín, bổ sung thêm các trụ đỡ băng tải và kiểm soát dòng khí đi qua khu vực lắng đọng liệu, các công việc này có thể thực hiện được trong vài ngày trong thời gian dừng theo kế hoạch.
Lắp đặt trên cao
Sử dụng một cần trục để nâng các chi tiết tới sàn thao tác trên cao, 5 nhân viên nhà thầu và một chuyên gia giám sát của Martin Engineering đã tiến hành tháo dỡ hệ thống cũ, lắp đặt các chi tiết mới và vệ sinh sạch sẽ khu vực trong chưa đầy 4 ngày. Sự quay vòng nhanh chóng này cho phép cải thiện thử nghiệm hệ thống trước khi kết thúc thời gian ngừng hoạt động.
Giá đỡ chịu va đập làm giảm bớt sự va chạm giữa liệu và băng, giảm bớt những nguy cơ gây hư hại băng nghiêm trọng. Thiết bị có các thanh UMHW được tạo rãnh có độ ma sát thấp đỡ các gờ băng tải và giữ ổn định tuyến băng tải. Điều này tránh cho băng khỏi bị chùng xuống và nảy lên do các con lăn chịu va đập gây ra và giảm bớt nhu cầu thay thế các chi tiết con lăn bị vỡ mà có thể làm gia tăng độ ma sát lên băng. Thiết kế dạng ‘hộp’ cho phép lật từng thanh lên sử dụng tiếp cho tuổi thọ mòn lần thứ hai.
Khi được chất tải ở tốc độ cao, liệu nóng va vào phần thành bao che có thể ăn mòn nhanh chóng kim loại và tạo ra các lỗ mà qua đó liệu tràn có thể thoát ra ngoài. Tấm lót chịu mài mòn bên ngoài bổ sung thêm một lớp bảo vệ và có thể thay thế được từ bên ngoài ống chute. Các thiết kế trước đây chỉ thiết kế khoảng không lối vào cho một công nhân vào sử dụng đèn hàn thiếc để tháo dỡ tấm lót. Hiện tại, công việc này có thể được thực hiện an toàn bằng các công cụ đơn giản từ phía ngoài phần bao che.
Đi kèm theo tấm lót chịu mài mòn ở bên ngoài phần bao che là các tấm viền làm kín. Hệ thống làm kín kép này được làm từ hỗn hợp cao su durometer 70 EPDM (ethylene propylene diene monomer) ngăn ngừa liệu tràn nhờ duy trì được lớp chắn bụi hiệu quả. Phần làm kín ban đầu được kẹp vào thành ống chute, cùng với một van lật thứ cấp tự điều chỉnh bố trí ở phía ngoài để bảo vệ thêm.
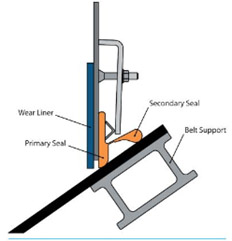
Tấm lót chịu mài mòn, tấm chắn và tấm làm kín.
Theo sau puli cuối (tail pulley) dẫn vào giá đỡ chịu va đập là các con lăn căng băng được lắp trên đường ray, mà cũng đỡ băng ở giữa các giá đỡ. Việc thay thế các con lăn căng băng được thực hiện dễ dàng, vì các chi tiết được đẩy trượt ra ngoài thanh sườn để bảo dưỡng bên ngoài. Việc ngăn ngừa không cho băng bị võng xuống là quan trọng để tạo ra độ kín khít và khống chế sự tràn liệu. Các con lăn căng băng được đặt đúng vị trí giữa các giá đỡ giúp đảm bảo đường băng chạy suôn sẻ ở các vị trí chất tải và lắng đọng liệu.
Các tấm chắn bụi ở phía trước và phía sau ống chute làm giảm sự phát thải bụi.
Hai giá đỡ khối trượt đưa liệu qua khu vực lắng suôn sẻ, giúp định tâm cho liệu. Giống như các giá đỡ chịu va đập, các giá đỡ này có các thanh được tạo rãnh rộng hơn giúp chống lại sự va chạm và chèn lấn liên quan tới các con lăn căng băng. Được bố trí lần lượt cùng với các con lăn căng băng lắp trên đường ray ở giữa, chúng làm gia tăng độ kín khít cùng với các tấm che ở mép băng giúp ngăn ngừa sự cố tràn liệu.
Các tấm chắn bụi ở hai đầu ống chute kiểm soát dòng khí chảy rối hình thành trong quá trình chất tải khỏi thoát ra ngoài ở cả hai đầu ống chute và mang theo liệu bay lơ lửng đi cùng với nó. Nhờ kiểm soát dòng khí, liệu rơi xuống băng nhanh hơn và giữ lại được nhiều sản phẩm hơn.
Các kết quả đạt được
Gần một năm kể từ khi lắp đặt, các nhân viên vận hành báo cáo hiệu suất đã tăng lên và giảm đáng kể sự cố tràn liệu, nhận xét rằng tình trạng liệu chất đống trên lối đi đã giảm đi, và rằng ở chính khu vực này đã bớt bụi hơn, độ an toàn tăng lên xung quanh điểm trung chuyển.
Sự hư hại băng tải như các lỗ và sự đứt rời mối nối đã không còn là vấn đề nữa kể từ khi lắp đặt đến nay, giảm bớt đáng kể chi phí vận hành vì việc thay thế băng tải là một công việc rất tốn kém và tiêu tốn nhiều thời gian. Phần bao che vẫn giữ nguyên và được làm kín, liên tục kiểm soát liệu tràn. Việc tháo dỡ hầu hết các con lăn không tải ra khỏi toàn bộ điểm trung chuyển đã làm giảm bớt nguy cơ gây chấn động con lăn và hư hại do ma sát ở phía quay về của băng tải.
Nhà máy xi măng không còn cần đến đội ngũ vệ sinh cùng với xe téc chân không nữa, nhờ đó giảm bớt được giờ công cũng như chi phí choviệc thực hiện bảo dưỡng và dọn vệ sinh. Thiết bị của Martin đã góp phần làm cho khu vực này nhìn chung an toàn hơn và hiệu quả hơn
Nguyễn Thị Kim Lan dịch từ International Cement Reviews số tháng 12/2021
VLXD.org